article A Brief Recap of Reusable Rockets ~14 minute read
The Space Shuttle lifts off.
Credit:
NASA
One of the major advantages of the Shuttle when compared to other vehicles was its ability to launch both crew and cargo on the same flight. Today, no launch vehicle has the same capability, and there are no serious plans for a spacecraft that launches crew and cargo at once. Despite this advantage, the Shuttle was just too expensive, complex, and unsafe; and in 2011, the Space Shuttle program came to an end.
Reusable rockets aren’t new. Although SpaceX was the first company to successfully recover the first stage of an orbital-class rocket in December of 2015, reusable rockets have been considered since the 1960s. Even the Saturn V, the rocket that launched humans to the Moon, was the subject of multiple proposals that would enable partial recovery of the launch vehicle. In the end, none of these proposals were ever implemented.
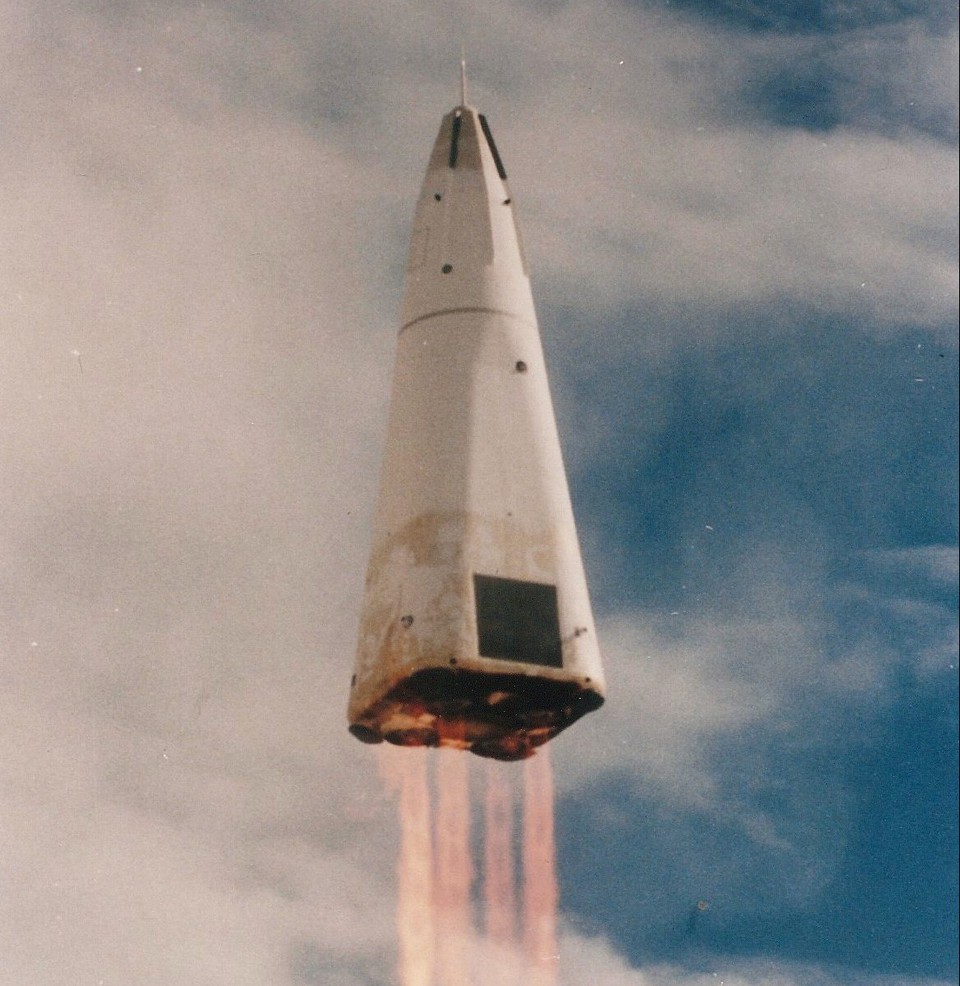
The DC-X on its fourth flight Credit: McDonnell Douglas
In the 1990s, McDonnell Douglas began testing the DC-X, an experimental testbed for building rockets capable of vertical landing and takeoff, or VTOL. The DC-X vehicle first flew in 1993, and over the next three years it flew eleven more times. These were all small hops of only one or two kilometers; the final flight reached an altitude of only 2.5 kilometers. Even though it never demonstrated high-altitude flights, it proved that building a VTOL rocket was possible.
The DC-X program was shelved when a landing leg failed to deploy and the rocket tipped over after landing, damaging the aeroshell. NASA did not have the budget to devote to the DC-X program, and it was cancelled in 1996. Several of the remaining DC-X engineers are now involved with Blue Origin, which is working on its own reusable rockets today.
Now, for an explanation of why it’s so easy to reuse airplanes and cars and why it’s so difficult to reuse rockets.
Rockets that reach orbit need to fly very, very fast. There is a huge difference between reaching space, which is only 100km above sea level; and orbit, which requires a velocity of at least 7.6 kilometers per second. That’s 22 times the speed of sound. The only way to get that fast is to bring a lot of fuel with you, and to bring fuel you need a place to store it.
At liftoff, modern rockets are about 90% fuel by mass. Of the remaining 10% mass, the useful payload is usually less than 30% (or 3% of the total vehicle mass at liftoff.) The lighter the rocket, the heavier the payload it can launch into orbit. Everything you add to make a rocket reusable also reduces the maximum payload.
This has made reusable rockets a difficult pill to swallow. The payload capacity would need to be cut nearly in half to make even the first stage reusable, and then you would need to prove that the stage could reliably land and fly again with minimal maintenance. It’s a huge financial gamble that might not even work out.
In 2001, Elon Musk wanted to get the public excited in Mars, to push Congress to increase funding for NASA. He decided to send a greenhouse to Mars, called Mars Oasis; in his words, it would “show great images of green plants on a red background” and “get the public excited [about Mars.]” The greenhouse itself would be relatively simple; but the rocket launch would not. Musk visited Russia three times, attempting to buy used ICBMs; however, they were far more expensive than he thought they would be. On the plane back to the United States after his last trip to Russia, he turned to aerospace consultant and friend Jim Cantrell and said, “I think we can build a rocket ourselves.”
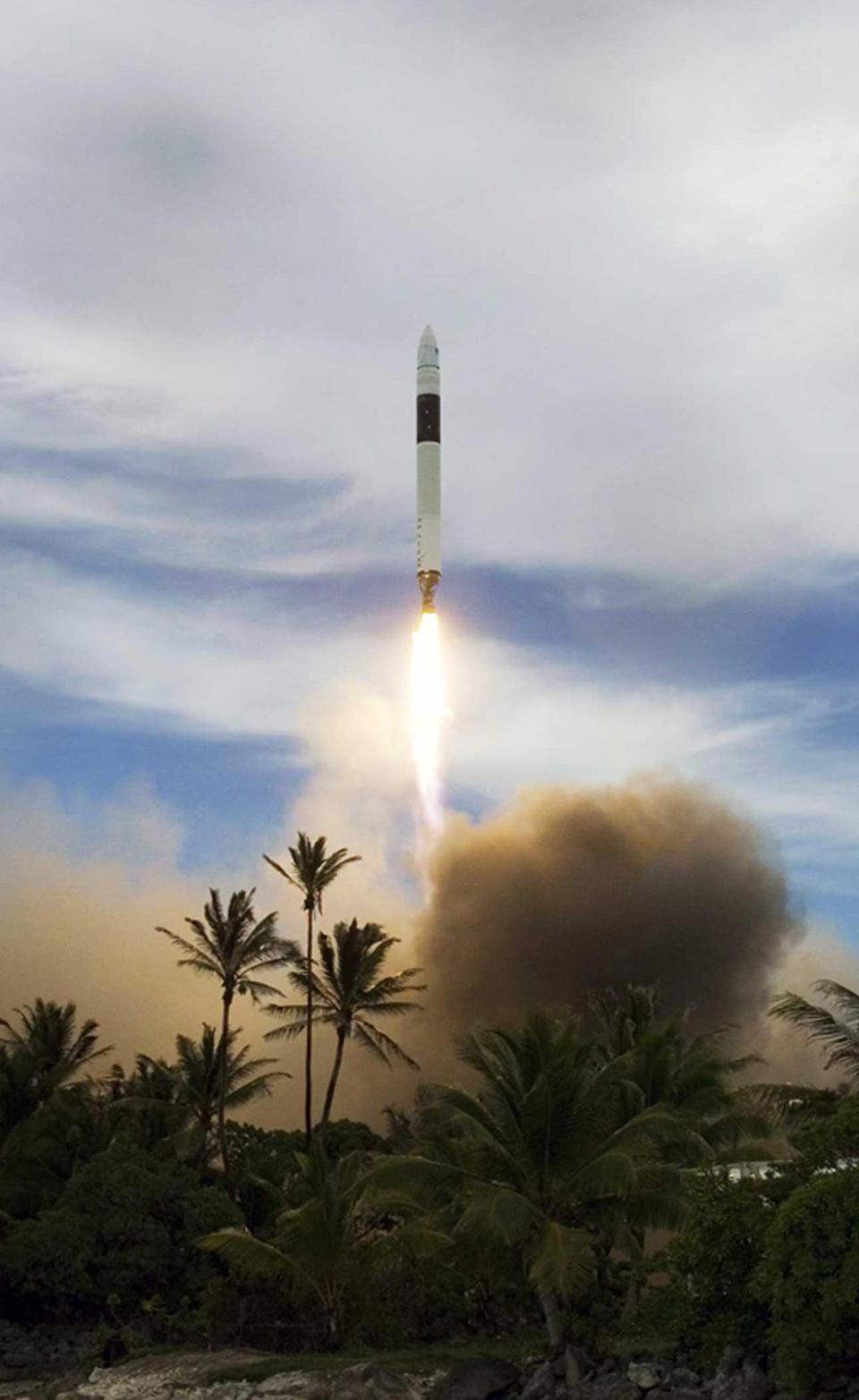
The SpaceX Falcon 1 lifts off from Omelek Island Credit: NASA
In 2002, Elon Musk founded SpaceX with the goal of making life multiplanetary. As he saw it, the issue was that expendable rockets had a fixed cost: because you needed to build a new rocket for each flight, you couldn’t distribute the manufacturing cost of the rocket across all of its flights. Passenger jets cost hundreds of millions of dollars, but the cost is spread out among all the flights. Reusable rockets were key to the dramatic launch price reductions that would make space more accessible.
But before SpaceX could tackle reusability, they needed to build a rocket that could reach orbit. Their first rocket, the Falcon 1, was a 21-meter tall two-stage rocket. Its maiden launch, in 2006, ended in failure after an engine fire; the rocket fell back into the ocean less than a minute after liftoff. The cause was eventually traced to a nut that had corroded after exposure to saltwater spray.
The next two launches did better, with Flight 3 nearly reaching orbit. At this point, though, SpaceX was running low on money for a fourth flight, and Elon had to personally fund the fourth launch of the Falcon 1.
At around the same time, SpaceX President and COO Gwynne Shotwell managed to win SpaceX a NASA contract for the CRS program. Under this contract, SpaceX was to be paid $1.6 billion for 12 resupply missions to the International Space Station. The other winner of the contract, Orbital ATK, was a defense supplier that had already demonstrated dozens of successful orbital launches. For SpaceX to win this contract before they had even reached orbit demonstrated the potential that NASA saw in the SpaceX engineers.
Thankfully, the fourth launch of the Falcon 1 went off without a hitch, as did the fifth. At this point, SpaceX decided to begin the design process on their new Dragon spacecraft and a new rocket: the Falcon 9. These were the vehicles that SpaceX would fly to the ISS under the NASA resupply contract; and in the future, SpaceX would modify the Dragon and Falcon 9 to fly crew.
Although the Falcon 1 never flew again, its legacy lives on in the Falcon 9. Many of the key technologies in the Falcon 9 were proven in the Falcon 1, including the Merlin engines and the tank construction. The Falcon 1 flights even experimented with recovering the first stages with parachutes, but the boosters kept breaking up before the parachutes were even deployed. These lessons were very valuable when SpaceX decided to design recovery systems for the Falcon 9.
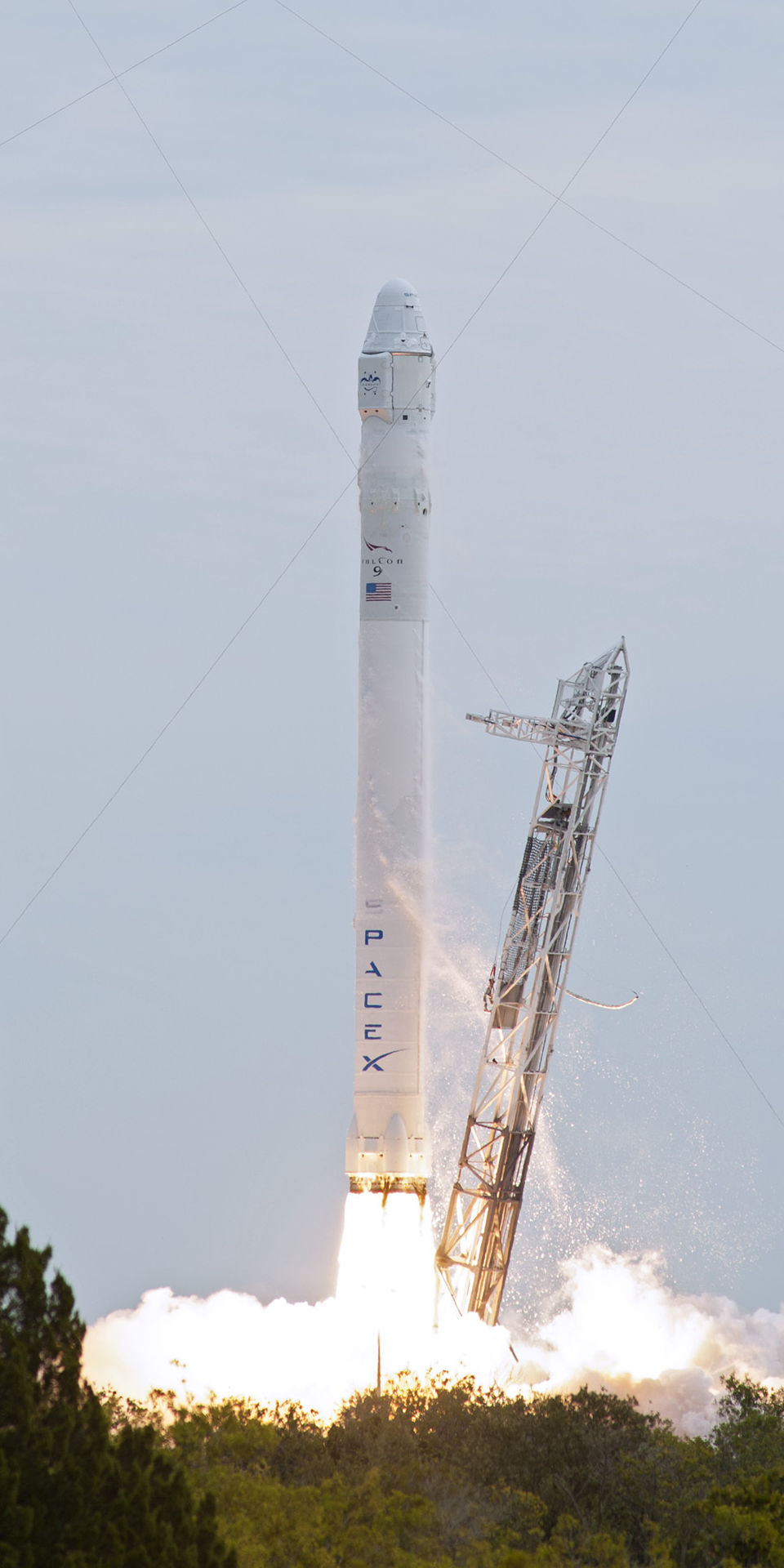
The CRS-2 Falcon 9 lifts off, carrying the Dragon capsule to the ISS. Credit: NASA
The Falcon 9 v1.0 is a two-stage rocket standing 54 meters tall. It’s large enough to launch cargo and crew to the International Space Station with the Dragon capsule, and because it has nine engines, it can still complete its mission even if an engine fails during launch.
The Falcon 9 launched for the first time in 2010 and performed flawlessly, deploying a dummy spacecraft into low-Earth orbit. Like on the Falcon 1, SpaceX tried to put parachutes into the Falcon 9 first stage; once again, the stages broke up before the parachutes even had a chance to deploy.
So, in 2011, SpaceX announced that instead of using parachutes to recover the first stage, they’d use actively-guided propulsive landing. This means they’d use the Falcon 9’s engines to guide the booster back to land. This would involve several different maneuvers; first, the booster would need to turn back towards land and restart three engines for the boostback burn; then, it would turn to face engines-first and restart the same three engines to slow it down in the entry burn; finally, as it approached its landing pad, it would start up the single center engine for the landing burn; then, seconds before landing, it would deploy its four landing legs and touch down on land only a few kilometers from its launchpad.
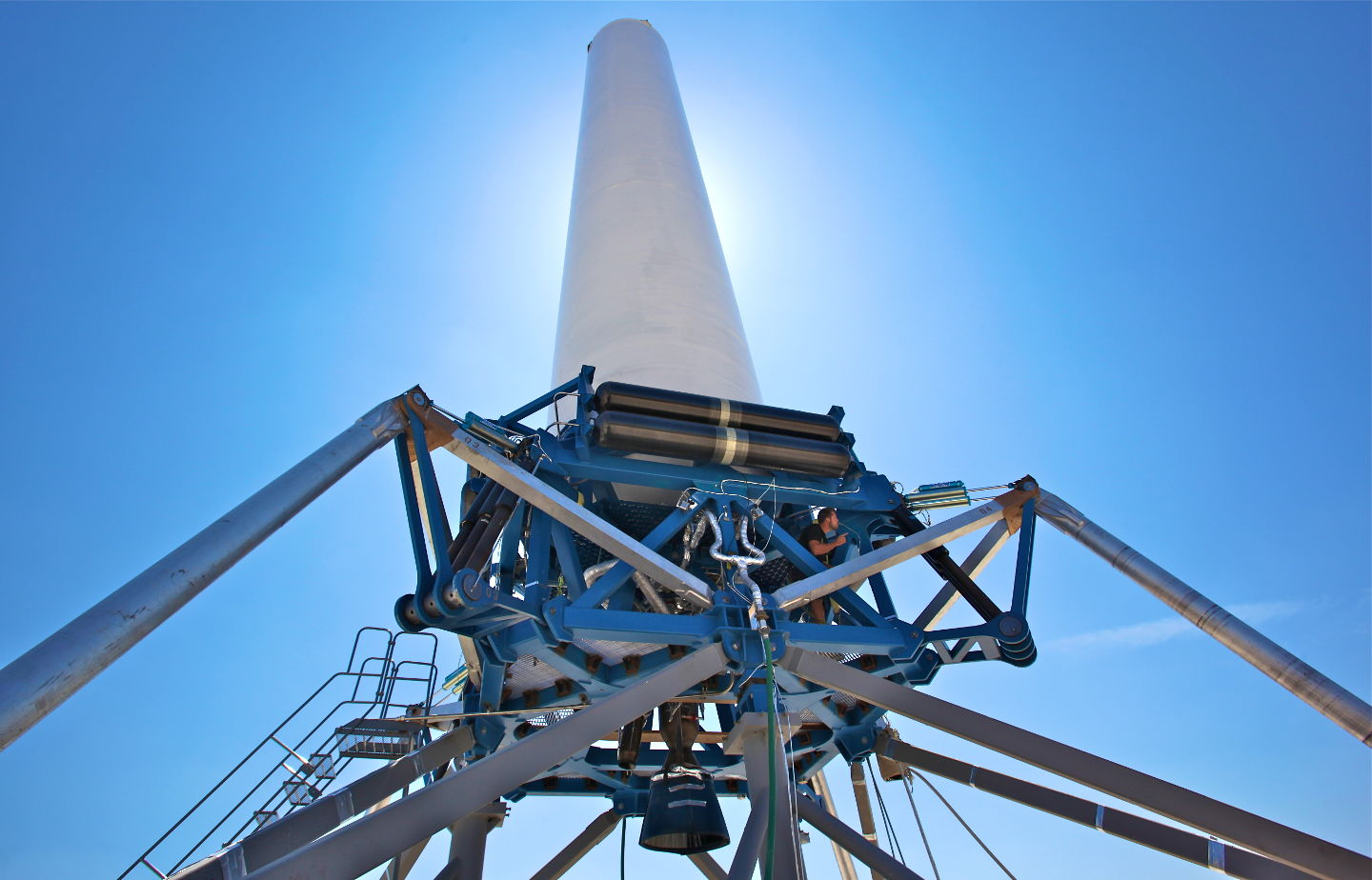
The Grasshopper testbed, in 2012. Note the mechanic standing next to the landing leg. Credit: Steve Jurvetson
However, such a plan would need a lot more fuel. Normally, the first stage engines are shut down and the stages separated only when the fuel is nearly depleted. SpaceX would need to shut the engines off earlier than normal and leave a substantial amount of fuel onboard the first stage. This fuel would be used to reignite the engines to fly the booster back to land. It would also require very accurate control of the booster, or it would land dozens of kilometers off-target, or worse, hit the ground at Mach 1 and explode.
So SpaceX built an experimental rocket, called the Grasshopper. It made eight successful flights in 2012 and 2013, demonstrating accurate throttle and gimbal control of the engine. These flights were all small hops, similar to those made by the DC-X. The Grasshopper vehicle demonstrated stable hovering, horizontal diverts, and on its final flight, reached an altitude of over 700 meters. At this point, SpaceX had reached the limits of the Grasshopper, and the vehicle was retired and replaced with the more capable F9R-Dev1.
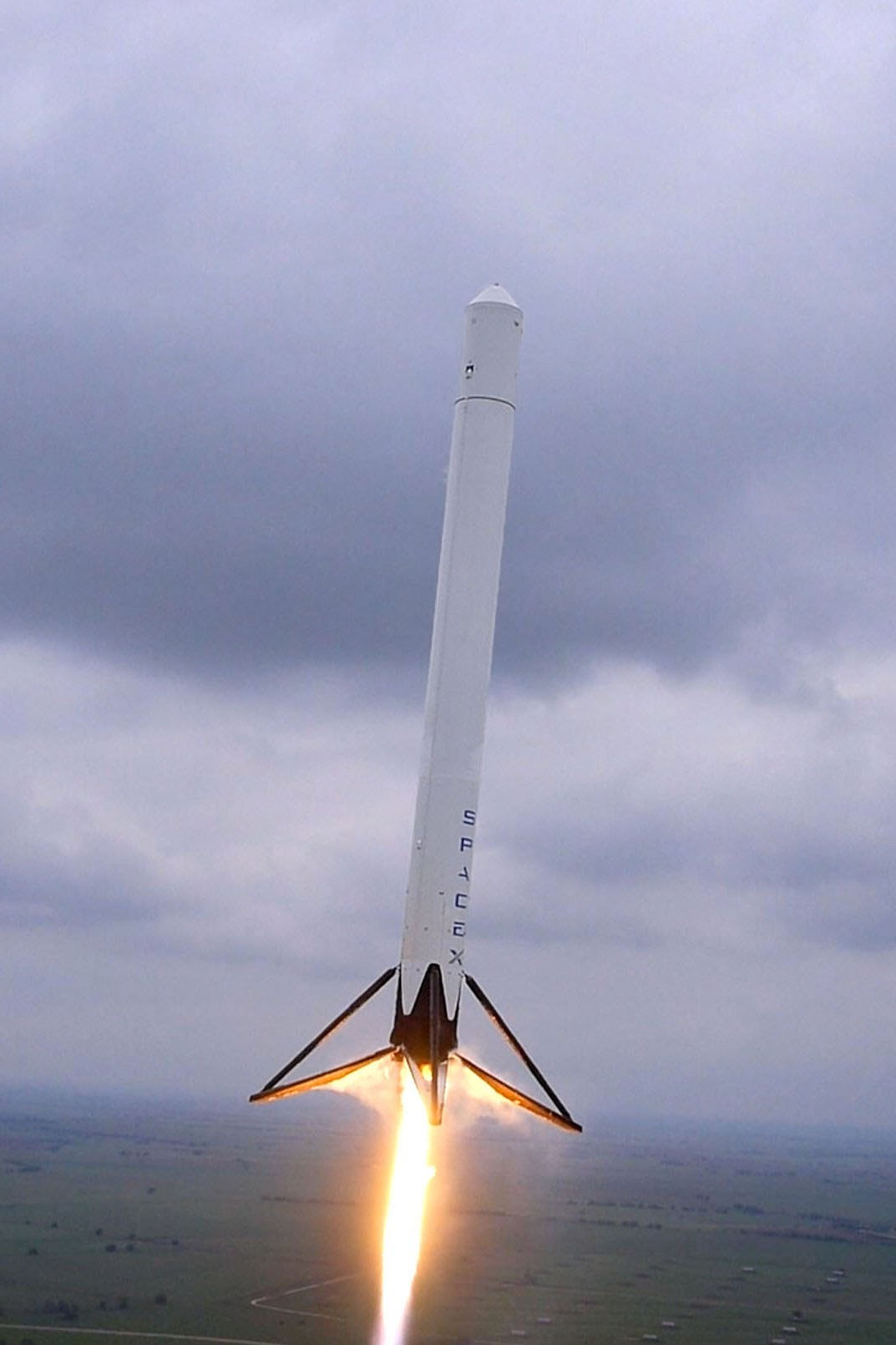
The F9R-Dev1 testbed in-flight. Note the four landing legs. Credit: SpaceX
The F9R-Dev1 was a more advanced version of the Grasshopper; where the Grasshopper featured custom landing legs and other hardware, the F9R-Dev1 was a mostly standard Falcon 9 v1.1 booster. Even the landing legs were the prototype carbon-fiber legs that would eventually be used on the Falcon 9. The F9R-Dev1 flew five times, reaching a peak altitude of one kilometer; on its final flight, a blocked sensor caused the vehicle to veer off course, and the flight termination system was triggered, ending the flight.
In 2013, SpaceX flew the first flight of a significantly larger Falcon 9 v1.1, with almost twice the fuel capacity, along with internal modifications that would allow legs and other hardware to be attached. Over the next few flights of the upgraded Falcon 9, SpaceX attempted to perform soft ocean landings to demonstrate the technology; the first successful landing was with the CRS-3 mission. The booster touched down on the ocean’s surface during a storm, and although it splashed down gently, it broke apart when it hit the ocean, as expected.
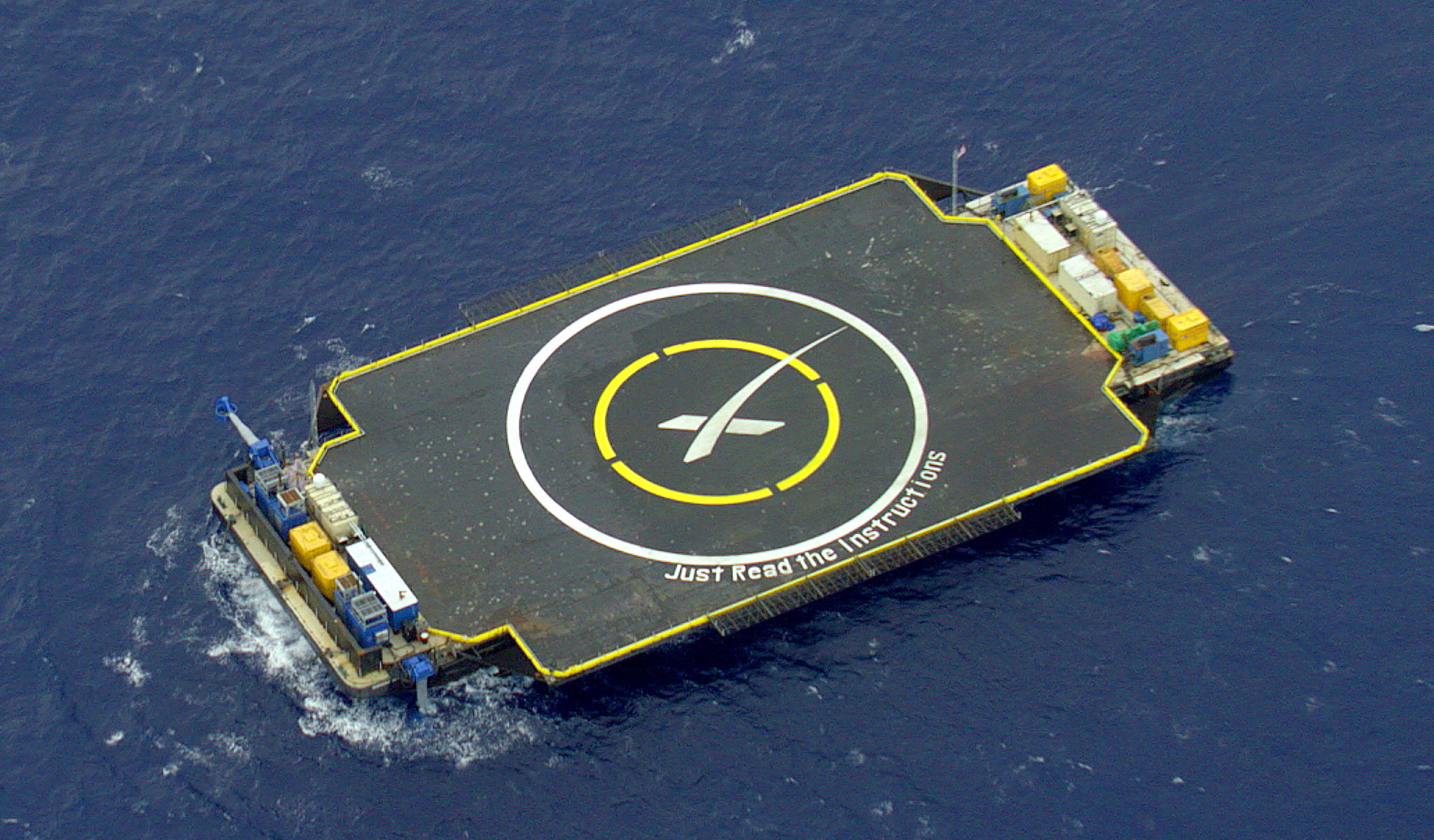
'Just Read the Instructions', SpaceX's first droneship. Credit: SpaceX
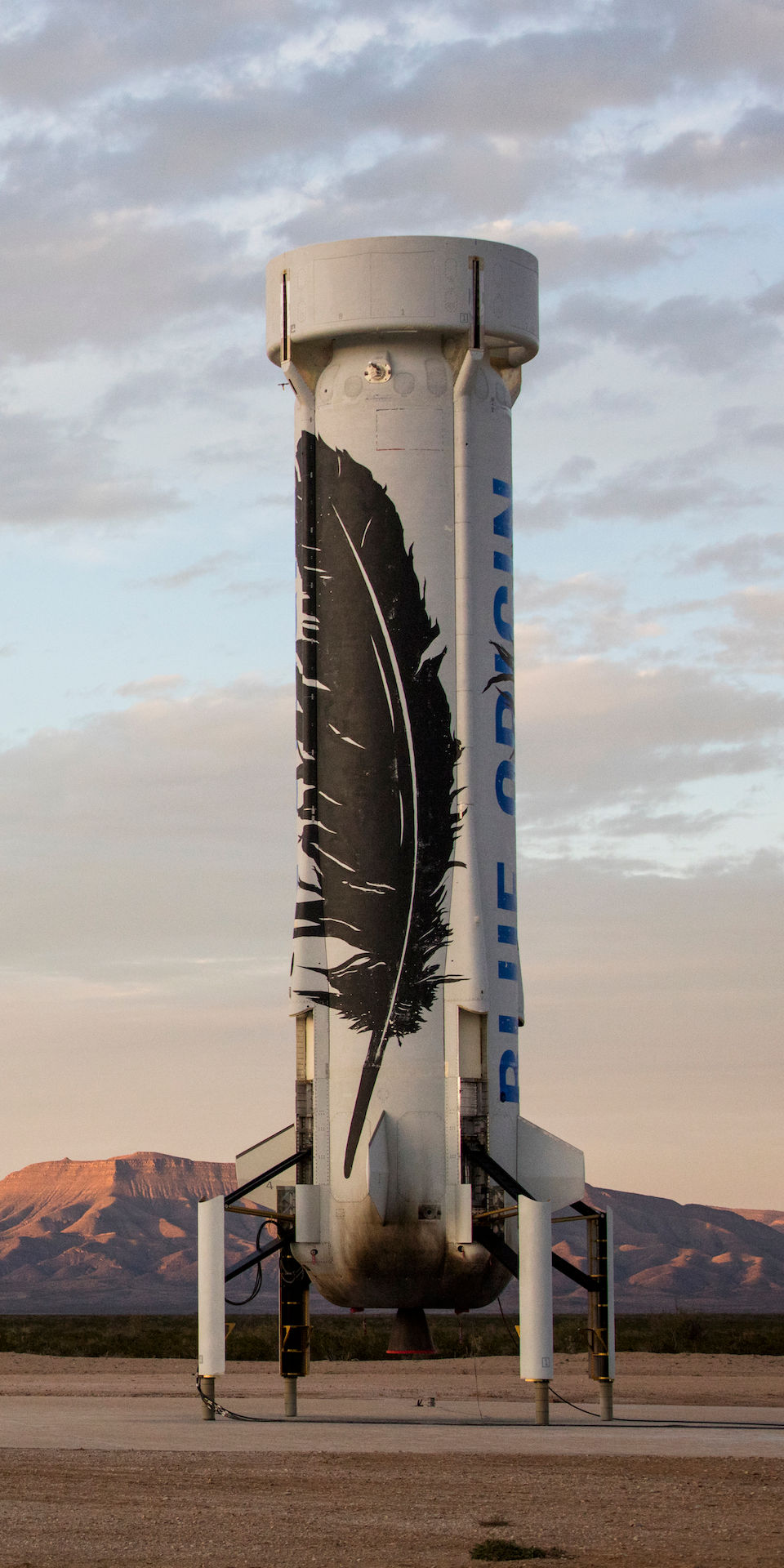
The NS2 booster, the first ever rocket to reach space and land vertically. Credit: Blue Origin
Next, SpaceX needed a place to land. They hadn’t yet built a landing pad, and they also hadn’t received permission to bring a rocket back to land. Ocean landings wouldn’t work; the booster was so tall that it would disintegrate when it fell into the ocean. So they modified a barge, converting it to a powered droneship, and painted a giant “X” on it. It was sent out into the ocean for the first time in 2015, for the CRS-5 mission.
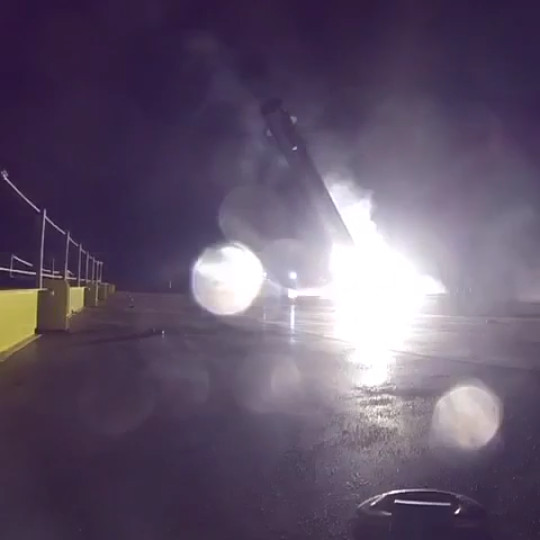
The CRS-5 booster smashing into JRTI Credit: SpaceX
The CRS-5 launch went perfectly, and the Falcon 9 booster performed all the necessary engine burns flawlessly; however, the grid fins used for maneuvering the booster ran out of hydraulic fluid, and the booster smashed into the droneship at highway speeds. Needless to say, the landing was not very smooth, and the only parts that came back were in a pile on the droneship, covered by a tarp.
The next attempt, with the CRS-6 mission, did far better. The booster performed perfectly, but when it was less than ten seconds from landing, an engine throttle valve got stuck, and the booster landed hard and tipped over seconds later. Just like CRS-5, they brought back the remains of the booster in a pile.
On the next launch, with the CRS-7 mission, the launch vehicle failed before there was a chance to attempt a landing, and the CRS-7 Dragon capsule was destroyed. SpaceX was grounded for several months while they solved the issues that caused the CRS-7 failure.
In the meantime, Blue Origin’s experimental test program, shrouded in secrecy for years, announced that their New Shepard rocket had become the first ever rocket to reach space and land vertically. The New Shepard booster, like the Falcon 9, was designed to be reusable; unlike SpaceX, Blue Origin had been planning to land their rockets propulsively from the start, and they had been quietly experimenting with it for over a decade.
The New Shepard vehicle is about 15 meters tall and has many different types of fins to stabilize and control the vehicle as it returns to Earth; notably, at the bottom of the vehicle, there are four maneuvering fins; and at the top of the vehicle, there are drag brakes (to slow the vehicle) and wedge fins (to keep the vehicle stable) mounted to the ring fin.
Whereas the Falcon 9’s purpose is to launch payloads into orbit, the New Shepard is both a testbed and a space tourism platform. It’s capable of launching multiple space tourists to 100km and returning them safely, requiring far less energy than reaching orbit. For this reason, the New Shepard is fully reusable; both the crew capsule and the propulsion module can be recovered and reused for future flights.
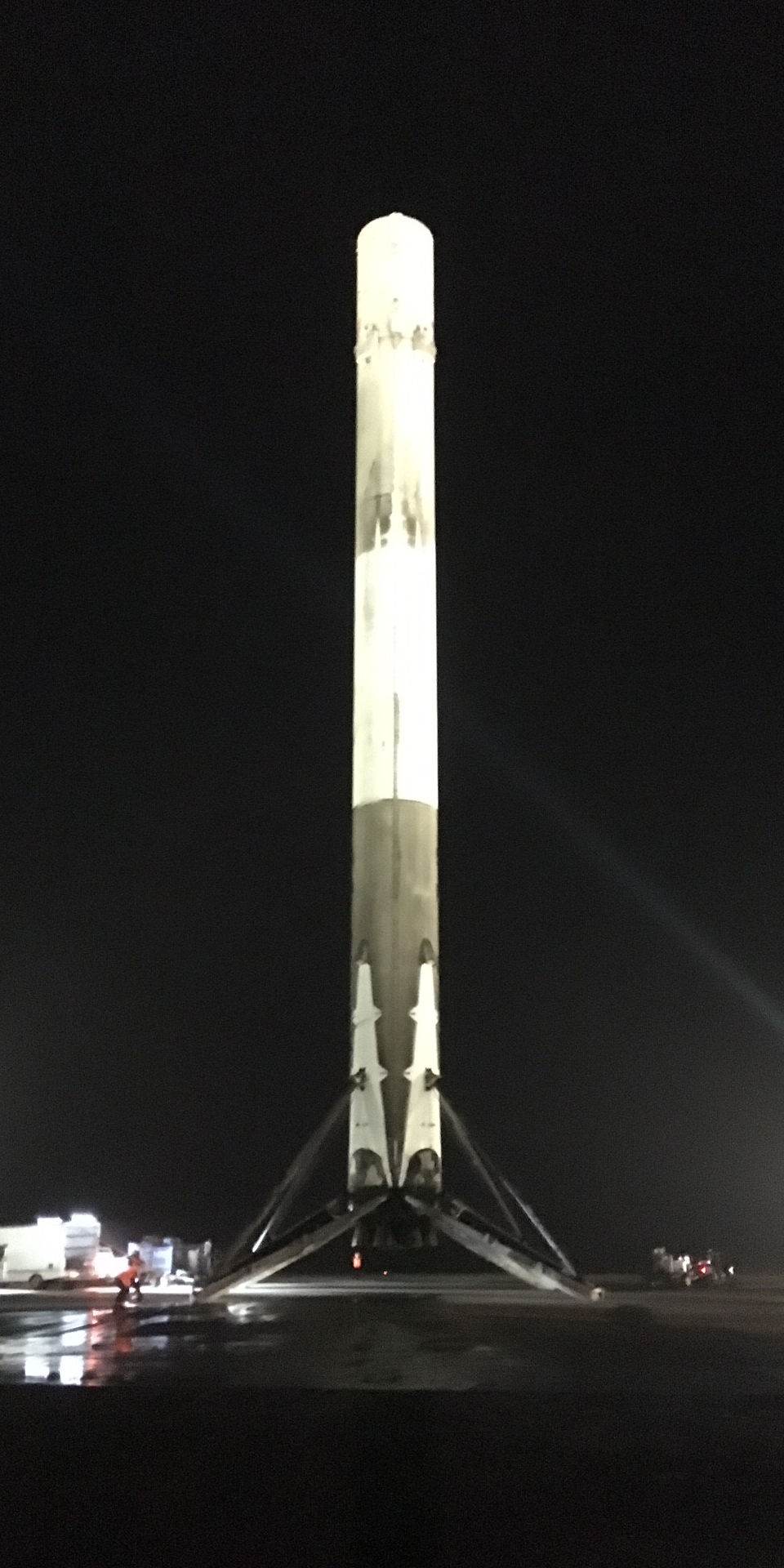
The Orbcomm OG2-M2 booster after its landing. Credit: SpaceX
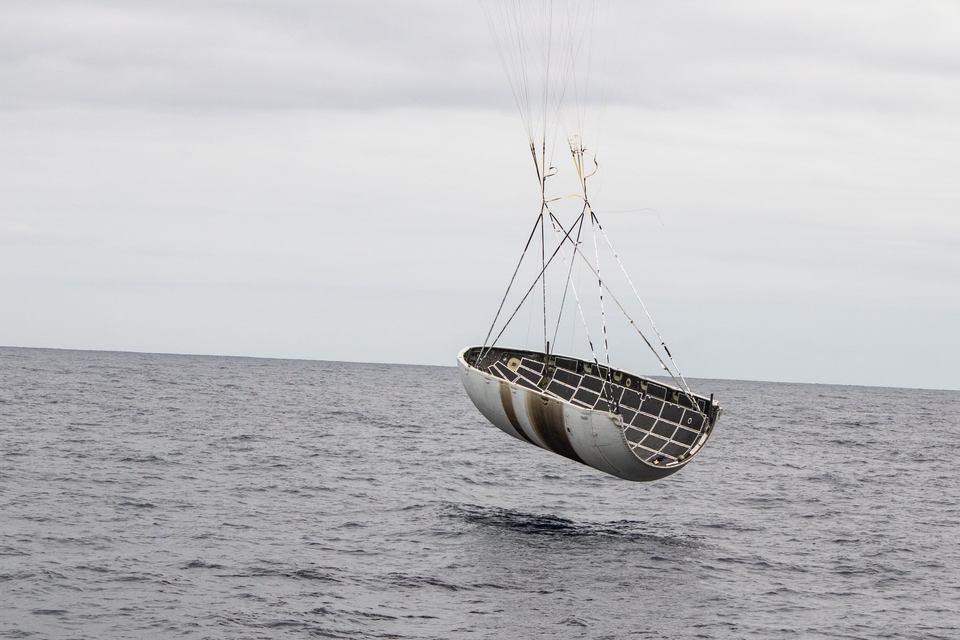
The Iridium-6 fairing just misses Mr. Steven, SpaceX's fairing recovery ship Credit: SpaceX
SpaceX’s next mission was the Orbcomm OG2-M2 launch; the first flight after the CRS-7 inflight breakup. It was also the first Falcon 9 to be powered by densified propellant; this, combined with the lightweight payload, meant that the Falcon 9 booster could return to the launch site.
The flight was picture-perfect, and less than ten minutes after liftoff, the booster touched down smoothly and softly at SpaceX’s landing pad at Cape Canaveral, marking the world’s first recovery of an orbital-class booster.
On March 30, 2017, SpaceX made history when they launched a rocket with a reused booster for the SES-10 mission, cementing SpaceX’s place in history as the first company to ever refly a recovered booster from an orbital-class launch vehicle. This marked a major milestone in the journey for reusable rockets.
Over the next few months, SpaceX continued to recover every core they could, and so far, they’ve recovered 25 more boosters, by land and by sea. Two of these cores were converted into Falcon Heavy side boosters. Alongside a brand-new center core, they launched the Falcon Heavy into space, along with its test payload: Elon’s original Tesla Roadster. The side boosters both flew back and landed at Cape Canaveral, about 100 meters and 3 seconds apart.
While it’s not economically sensible to recover and reuse the Falcon 9 upper stage, SpaceX is working hard at recovering the Falcon 9 fairings. Combined, they cost about $6 million (about 10% of the total cost of the rocket), and they take up a substantial amount of floor space in the factory to build.
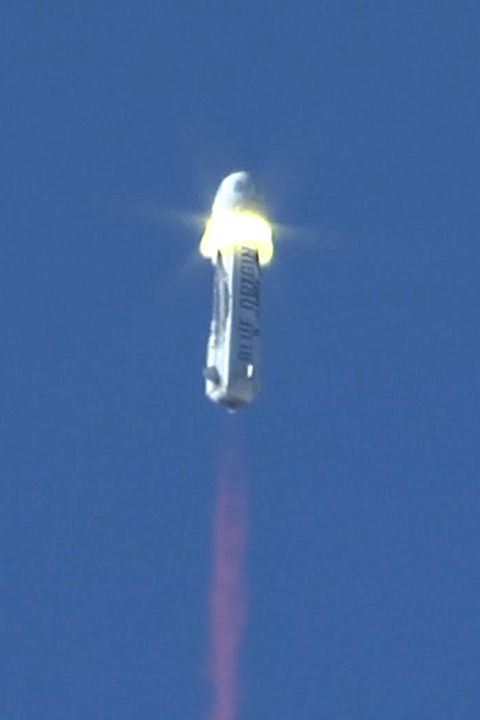
The NS2 booster, underneath the crew capsule at the moment of abort motor ignition. Credit: Blue Origin
In September of 2016, SpaceX announced their Interplanetary Transportation System, a rocket SpaceX hopes will begin the colonization of Mars. Both the first and second stages will be recovered and reused on every launch, dramatically reducing launch prices and opening up whole new worlds of human space exploration. SpaceX plans to reuse the booster a staggering 1,000 times; the propellant tanker and Mars lander are planned to be reused 100 and 12 times, respectively. These numbers bring Mars colonization within reach for the first time ever.
The final flight of the Blue Origin NS2 vehicle was in 2016, with the crew capsule performing an in-flight abort to verify the safety of the crew in the case of a booster failure. Miraculously, the booster survived the heat and debris from the solid rocket motor exhaust, then proceeded to continue its flight to space. Only a few minutes later, it performed a smooth landing on its landing pad. The booster was retired, and Blue Origin plans to perform more test flights this year. They’re planning to fly crew by the end of 2018.
Recently, Blue Origin unveiled their proposed orbital launch vehicle, the New Glenn. Like the Falcon 9, the first stage is built to be reusable; it will land itself on a ship in the ocean under its own engine power. Blue Origin is currently building a factory for the New Glenn at Cape Canaveral, and they hope to perform the first flights of the new vehicle by 2020.
With Blue Origin and SpaceX both demonstrating that booster reuse is possible, it now falls to the rest of the industry to follow along. Soon, the price for a launch on a reused rocket will drop, and the entire launch industry will need to lower their prices to remain competitive. I, for one, cannot wait for the low-cost future of spaceflight, where launches don’t cost tens or hundreds of millions of dollars; where you don’t need to be a giant international corporation to launch your satellites.
And just maybe, a future where your address will need to specify a planet.